Hollow objects can be easily created using rotational molding, sometimes referred to as rotomolding, a plastic molding technique. While the most common thermoplastic material used for plastic rotational molding is polyethylene, other materials include polypropylene, polyvinylidene fluoride, nylon and polyvinyl chloride Although it uses a casting technique, it does not use pressure like the majority of other plastics manufacturing techniques. Read More…
As a full-service rotational molding company, Roto Dynamics is your source for high quality, custom rotomolded products. Since our inception, we have continued to earn success by closely working with our customers, developing innovative and tailored solutions. We are with you every step of the way, from design and development to production and assembly. For a complete view of our capabilities and ...
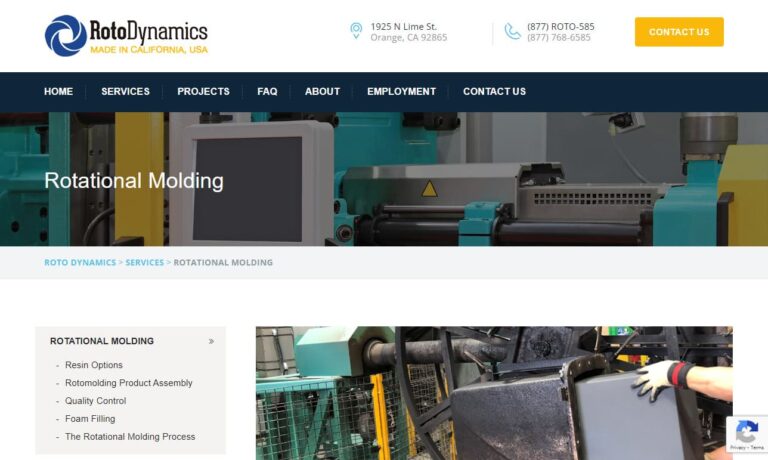
We are a custom manufacturer of rotationally molded products. Our state of the art technology creates precise, cost effective and dependable products. Whether your order is large or small, we want to be sure you are satisfied.
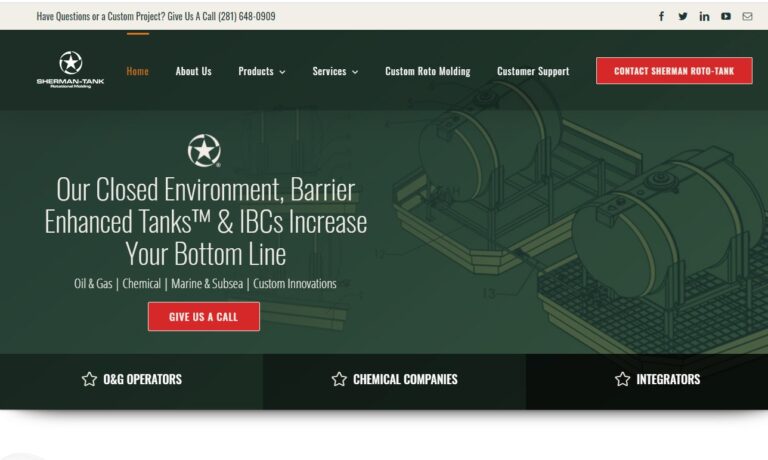
Western Industries Plastic Products, LLC, specializes in large-part plastic blow molding. We provide expertise and services in product design, process improvement, and product assemblies. We offer our customers comprehensive services and turnkey opportunities to achieve their specific project goals. We can assist with: R&D, product design, product improvement, and secondary-fixture design. For...
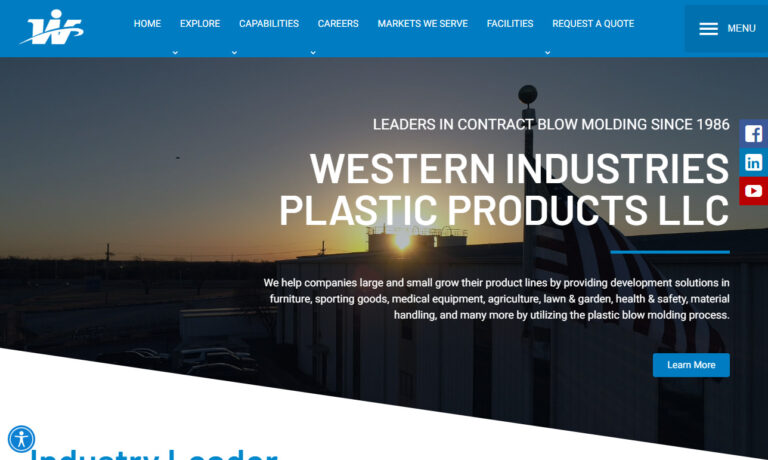
We provide outstanding custom plastic rotational molding. Our teams offer short lead times and we will assist you from concept to production. All of our materials and designs are FDA approved and we can handle the most complex projects. We are your one stop shop for all of your rotational molding needs. Give us a call today to learn more information!

Michiana Rotational Molding provides unparalleled rotational molding services that ensure efficient design, innovation, and functionality. Based in southwest Michigan, the company offers engineering, prototyping, finishing, design consulting, and quality control services. It has experience creating solutions for clients in the marine, home and garden, RV, and material handling industries and more ...
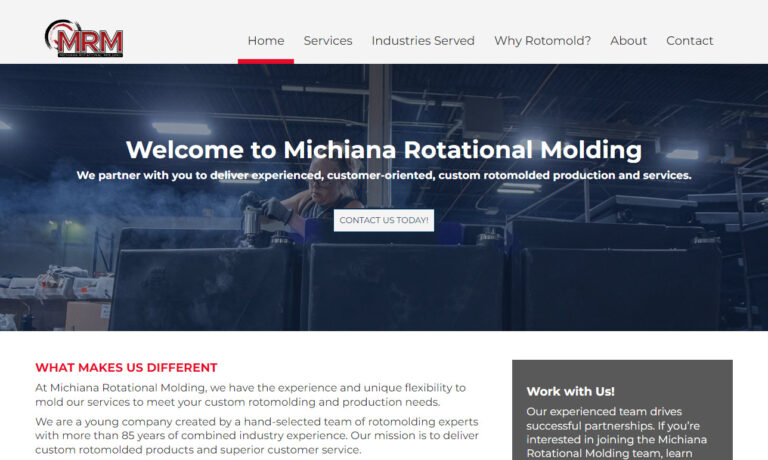
Our warehouses and equipment are designed to protect the quality and condition of the rotationally molded plastic products we sell and process. Our facilities feature state of the art equipment, and are run by a team of dedicated staff members who will help you find what you need. Contact us today!
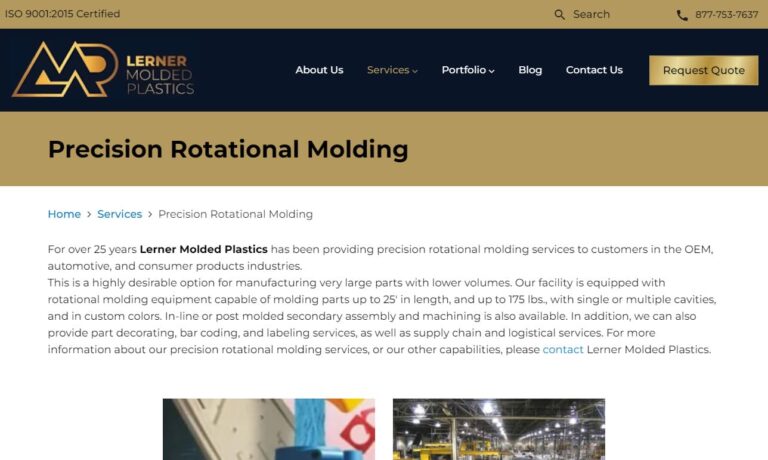
United States Plastic Corp. manufactures and distributes some 25,000 plastic items serving over 85,000 clients operating in a factory five acres under roof. Our major product is manufacturing plastic tanks, the distribution of bottles, carboy and plastic containers. This also includes plastic sheet, rods, tubes, flexible tubing and thousands of plastic fittings.
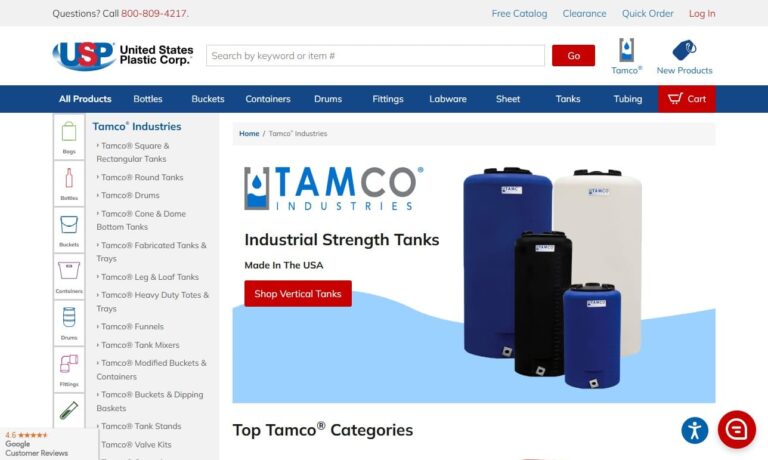
More Plastic Rotational Molding Companies
Due to the fact that the method's molds do not need to bear pressure, they may be created relatively cheaply for short production runs. Numerous different goods are manufactured using rotomolding. The method gives the product designer a great deal of creative freedom because virtually any shape can be created. There are literally thousands of uses, and there are virtually no size restrictions on moldings.

Plastic Rotomolding Process
The underlying principle of rotational molding is quite simple. A hollow mold that is normally made out of sheet steel or cast aluminum is filled with a plastic component, usually in powder form. Closed, the mold is slowly rotated on two axes. The polymer then progressively melts while being heated in an oven, "laying-up" on the inside of the rotating mold.
Once the polymer powder has melted fully, the mold is transferred to a cooling station and chilled, usually with air but occasionally with a fine mist of water. The portion solidifies as the mold cools. The process is stopped, and the result is removed from the mold. Once the material has finally cooled down enough, it is then loosened away from the mold surface.
The material cannot be regulated in the same way as high-pressure techniques like injection molding because it is a casting process and there is typically no pressure involved. Numerous factors, including ambient temperature and humidity, type of mold, material specifications, and powder quality, can have an impact on production and the final product.

Materials Used in Plastic Rotomolding
- More than 80% of the polymers used in industries that use rotational molding are made of polyethylene. This is because it is inexpensive and simple to mold. In contrast to non-polyethylene polymers, which are difficult to ground, it is easily accessible in powder form. Additionally, it has low water absorption and strong chemical resistance.
- Low-Density Polyethylene (LDPE), Medium-Density Polyethylene (MDPE), and Polypropylene. One of the most adaptable polymers on the market, polypropylene is the second most processed plastic. It shares traits with both LDPE and MDPE. Its favorable characteristics include good fatigue, heat, and chemical resistance.
- Vinyl chloride monomer is a polymer of a substance called polyvinyl chloride. It is a robust and rigid plastic that can have a wide range of additives added to change its mechanical characteristics.
Advantages of Rotomolding
- Rotational molding is a highly-efficient molding technique that enables producers to build incredibly durable items with the fewest possible design restrictions as well as to produce them at comparably cheap costs and in an ecologically friendly way. Furthermore, it is simple to manufacture huge things economically and with minimum material waste.
- Rotational molding can quickly be set up, enabling small batch production to satisfy fluctuating demand. In general, it is relatively inexpensive compared to fabrication, fiberglass, injection, vacuum, or blow molding procedures since it helps to reduce stock holding and probable redundancy of stock.
- Another one of rotational molding's key advantages is its adaptability. It makes it possible to produce items with several layers, a range of styles, colors, and surface finishes with none of the polymer weld lines. To meet the stringent design and engineering requirements, rotomolding can handle not just inserts but also logos, recesses, spouts, bosses, and many other characteristics. Additionally, employing this technique allows for many product types to be combined on a single machine.
Applications of Plastic Rotomolding
- Carboys, gallon barrels, and plastic storage tanks for holding tiny to extremely large volumes of water and chemicals
- Syringes, oxygen masks, and squeeze bulbs are examples of laboratory and medical supplies
- Rotational molding is the only method of manufacturing material handling equipment such as sturdy crates, stackable pallets, containers, and insulated boxes.
- Planting-related gardening and agricultural equipment, such as pots, troughs, compost bins, and gardening carts
- Sanitary items like garbage cans, trash containers, and septic tanks
- Rock and roll molding machines are used to create rowing boats, canoes, buoys, and kayaks, among other marine vehicles and equipment for transportation and water activities.
- On roads and highways, you can see safety barricades, traffic cones, and other such objects.

Choosing the Correct Plastic Rotational Molding Company
To make sure you have the most productive outcome when selecting a plastic rotational molding company, it is important to compare at least 4 companies using our plastic rotational molding directory. Each plastic rotational molding company has a business profile page that highlights their areas of experience and capabilities and a contact form to directly communicate with the company for more information or request a quote. Review each plastic rotational molding company website using our patented website previewer to get an idea of what each company specializes in, and then use our simple RFQ form to contact multiple plastic rotational molding companies with the same message.